Home How to Hide Outlets in Backsplash? Expert Guide for Homeowners You can hide outlets...
Read MoreGranite Fabrication Services in Lowell, MA
Are you dreaming of flawless granite countertops but worried about poor fit or substandard craftsmanship? At SF Marble & Granite Inc., we specialize in delivering premium granite fabrication services in Lowell, blending artistry and engineering to create surfaces that last for decades. With over 10 years of experience, we are your trusted granite fabricator near Lowell, transforming raw granite slabs into stunning, custom countertops and surfaces for kitchens, bathrooms.
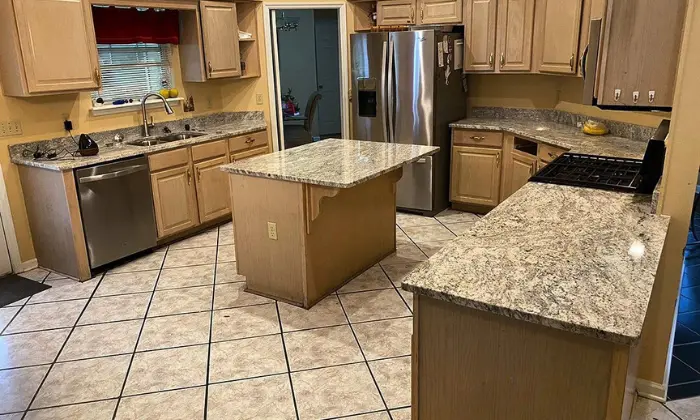
Our Granite Fabrication Services
We offer the following granite fabrication services in Lowell:
Granite Countertop Fabrication in Lowell
- Kitchen Countertops: Our heat-resistant and scratch-proof granite countertops are designed for busy households in Lowell. Available in a variety of colors and finishes, they add both beauty and functionality to your kitchen.
- Bathroom Vanities: Moisture-proof granite vanities are perfect for Lowell’s humid summers, offering durability with a touch of luxury.
- Outdoor Kitchens: Weather-tested granite surfaces withstand the elements, making them ideal for year-round backyard entertaining.
Custom Fabrication Specialties
- Custom edge profiles (Ogee, Bullnose, Dupont)
- Seamless sink cutouts for a polished look
- Thickness customization (2cm to 3cm) to match your design preferences
Whether you’re looking for unique designs or tailored solutions, our expertise in fabricating granite in Lowell ensures every piece is crafted to perfection.
Our 5-Step Granite Fabrication Process in Lowell
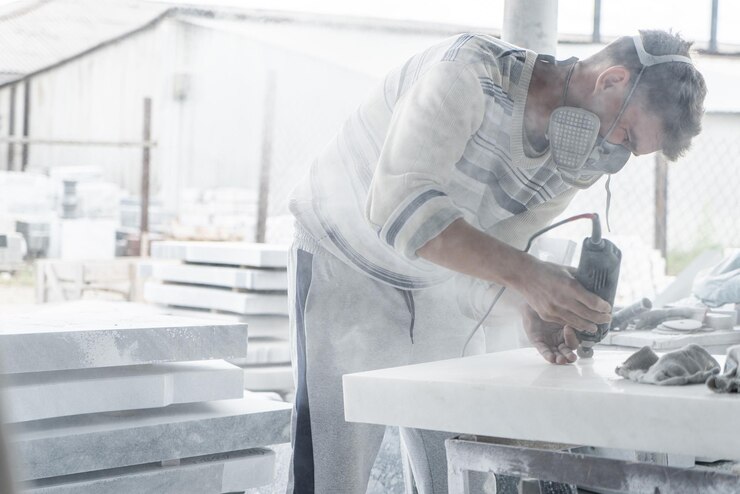
Choosing professional granite fabricators, like SF Marble Granite, offers numerous advantages that ensure your countertops and surfaces are not only visually appealing but also functional and durable. Here are the key benefits of opting for professional granite fabrication services:
Precision and Accuracy in Cutting and Shaping
Professional granite fabricators possess the expertise and specialized tools required to cut and shape granite with exceptional precision and accuracy. This level of craftsmanship ensures that every piece of granite is perfectly tailored to fit the designated space, whether it’s a complex kitchen layout, a uniquely shaped bathroom vanity, or a custom bar countertop. Accurate cutting and shaping also minimize the risk of errors, waste, and material loss, saving both time and money.
High-Quality Finish
One of the standout benefits of using professional granite fabrication services is the high-quality finish achieved through skilled polishing techniques. Fabricators meticulously polish the granite surfaces to enhance their natural beauty, bringing out the stone’s unique patterns and colors. A professionally polished granite countertop adds a luxurious and refined look to any kitchen or bathroom, significantly enhancing the overall aesthetic appeal of the space.
Longevity and Durability
Granite is renowned for its durability, but the quality of fabrication can significantly impact its lifespan. Professional fabricators understand how to handle granite properly, ensuring it is cut, shaped, and installed in a way that maximizes its strength and durability.
Properly fabricated granite countertops can withstand daily use, resist scratches, and are less prone to chipping or cracking, providing a long-lasting solution that retains its beauty and functionality for years.
Customized Solutions
Professional marble and granite fabricators offer customized solutions tailored to your specific needs and preferences. Whether you’re looking for a unique edge profile for your countertops, a specific thickness, or a custom design for a fireplace surround, professional fabricators have the skills and experience to bring your vision to life.
They work closely with clients to understand their requirements and offer expert guidance on choosing the right granite type, color, and finish that complements the existing decor.
Our Expertise in Marble and Granite Fabrication
At SF Marble Granite, we bring years of experience and expertise to the field of marble and granite fabrication. Our team of highly skilled professionals is dedicated to crafting beautiful and durable surfaces that elevate the aesthetics and functionality of any space.
As one of the leading providers of granite and marble fabrication services, we are proud of our ability to handle a wide range of projects, from simple installations to complex, customized designs.
Marble and Granite Fabrication
With a deep understanding of stone fabrication techniques, SF Marble Granite has earned a reputation for excellence in the industry. Our team is well-versed in the intricacies of working with both marble and granite, ensuring that each piece is meticulously crafted to meet the highest standards of quality and durability. Our extensive experience allows us to offer expert advice on material selection, design options, and the best practices for maintaining and caring for natural stone surfaces.
Expertise in Handling Complex Projects
At SF Marble Granite, we are equipped to handle projects of all sizes and complexities. From intricate kitchen countertops and elegant bathroom vanities to custom fireplace surrounds and outdoor kitchen surfaces, we have the skills and resources to bring your vision to life. Our team is experienced in tackling challenging projects that require precision cutting, detailed shaping, and seamless installation, ensuring a flawless finish that enhances the overall look and feel of your space.
Delivering Customized Granite and Marble Products
We understand that every project is unique, and that’s why we specialize in delivering customized granite and marble products tailored to your specific needs and preferences. Whether you’re looking for a particular color, texture, or edge profile, our team will work closely with you to design and fabricate the perfect stone surface for your home or business. We pride ourselves on our ability to create one-of-a-kind pieces that reflect your style and complement the existing decor of your space.
At SF Marble Granite, our commitment to quality craftsmanship, attention to detail, and exceptional customer service set us apart as trusted marble and granite fabricators. We are dedicated to transforming your vision into reality with beautifully crafted stone surfaces that stand the test of time.
Benefits of Hiring Lowell’s Top Granite Fabricator
Given are the benefits of hiring the top granite fabricator in Lowell:
Precision Cutting
Our advanced CNC machines ensure millimeter accuracy during cutting and shaping especially important for older homes in Lowell with uneven walls or unique layouts.
Durability Guarantee
Properly fabricated granite resists cracking and chipping even under extreme conditions. Our expertise ensures that your investment lasts for years to come while maintaining its beauty.
Local Showroom
Visit our showroom in Lowell to explore over 100 high-quality granite slabs in various colors and patterns. Our experts will guide you through the selection process to find the perfect slab for your project.
Why Choose SF Marble & Granite Inc.?
Local Expertise
As your reliable granite fabricators and installers near Lowell, we understand the unique architectural styles and climate challenges of the area. Whether you own a historic Colonial home or a modern property, our team ensures precision and durability in every project.
Full-Service Solutions
From design consultation to seamless installation, we provide end-to-end services as a top granite countertop fabricator in Lowell. Whether it’s a kitchen remodel, bathroom upgrade, or an outdoor kitchen project, we’ve got you covered.
10+ Years of Craftsmanship
With over a decade of experience serving Lowell, Chelmsford, Billerica, and surrounding areas, we’ve completed more than 500 projects. Our reputation as the go-to granite fabricator near Lowell is built on quality craftsmanship and exceptional customer service.
Ready for Flawless Granite Surfaces?
At SF Marble & Granite Inc., we take pride in being the leading provider of custom granite solutions in Lowell, MA. Whether you’re upgrading your kitchen or designing an outdoor space, our team is here to bring your vision to life with precision-crafted granite surfaces.
FAQs
What Are The Benefits Of Using Granite For Fabrication?
Granite is a durable and attractive natural stone that is resistant to heat, scratches, and stains. It also adds value to a property and has a unique, natural look that cannot be replicated by man-made materials.
What Types Of Products Can Be Made From Granite?
Granite can be used to create a wide range of products, including countertops, vanities, flooring, backsplashes, fireplaces, and decorative pieces such as statues and columns.
How Is Granite Fabricated Into Countertops?
Granite countertops are typically fabricated through a process that involves templating, cutting, edging, polishing, and installing. The process may also include the addition of sink cutouts and edge profiles.
How Long Does It Take To Fabricate Granite Countertops?
The fabrication process for granite countertops typically takes anywhere from one to two weeks, depending on the complexity of the project and the availability of materials.
Our Services
Contact Us
- 755 Dutton St. Lowell-MA 01854
- Phone: 978-459-5823
- FAX: 978 459 5827
- smgranite@hotmail.com
Our Blogs
The Guide to Choosing the Perfect Backsplash Color for White Cabinets
Home The Guide to Choosing the Perfect Backsplash Color for White Cabinets White cabinets have...
Read MoreRainforest Brown Marble: Nature’s Masterpiece for Timeless Interiors
Home Rainforest Brown Marble: Nature’s Masterpiece for Timeless Interiors Rainforest Brown Marble is a breathtaking...
Read More